Casa Mendes Gonçalves, a leader in high-quality vinegars, condiments, and sauces, used Prosys OPC UA Forge to streamline their industrial automation. By enabling real-time data monitoring and integrating diverse systems, Forge has helped the company improve efficiency and make data-driven decisions. This has already led to tangible benefits, such as detecting and fixing compressed air leaks, optimizing electricity usage, and preventing an unnecessary €110,000 investment in a steam boiler. This case study highlights how Forge provided valuable operational insights, reducing costs and enhancing factory performance.
About Casa Mendes Gonçalves
Casa Mendes Gonçalves, founded in 1982 and headquartered in Golegã, Portugal, is a leading producer of vinegars, condiments, and sauces. With a workforce of over 400 employees, the company exports its products to 31 countries, including Angola, Morocco, and Spain. Demonstrating a strong commitment to sustainability, Casa Mendes Gonçalves has implemented measures that have reduced energy consumption by approximately 7.8%. The company also emphasizes innovation, with a dedicated “Centre of the Future” team focused on exploring new market trends and product development. Their production capabilities are extensive, boasting 30 packaging lines and an annual output of over 14,000 tonnes of vinegar and 17,000 tonnes of sauces. This combination of tradition, quality, and forward-thinking has established Casa Mendes Gonçalves as a significant player in both local and global markets.
Challenges
With machinery from multiple manufacturers, Casa Mendes Gonçalves faced challenges in managing real-time data from diverse systems. They needed a reliable way to monitor production lines, store data efficiently, and visualize performance metrics in one centralized platform. These challenges made it difficult to achieve optimal productivity.
Solution Implementation
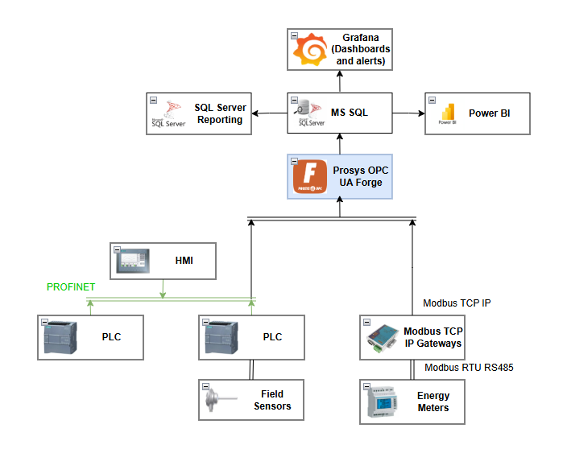
To visualize and analyze this data, the company utilized Grafana dashboards, which were deployed locally on their server alongside OPC UA. These dashboards provided real-time insights into machine performance and production status, making it easier to track operational efficiency. The integration process involved configuring Forge to connect with diverse PLCs and devices, setting up automated data logging, and developing customized dashboards tailored to the factory’s needs.
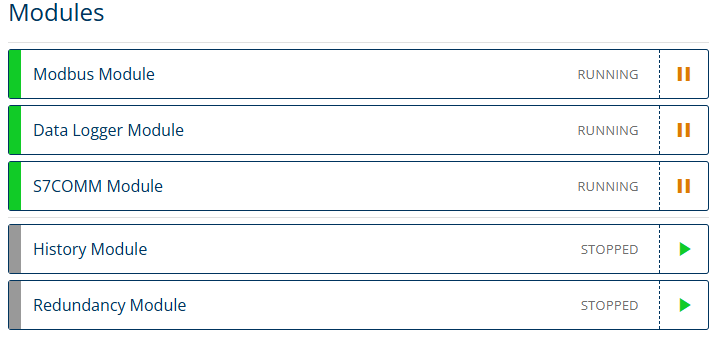
The user-friendly nature of both Forge and Grafana streamlined the implementation, even for team members new to the system. With this solution in place, Casa Mendes Gonçalves continues to refine and optimize productivity, leveraging data-driven decision-making to enhance factory operations.
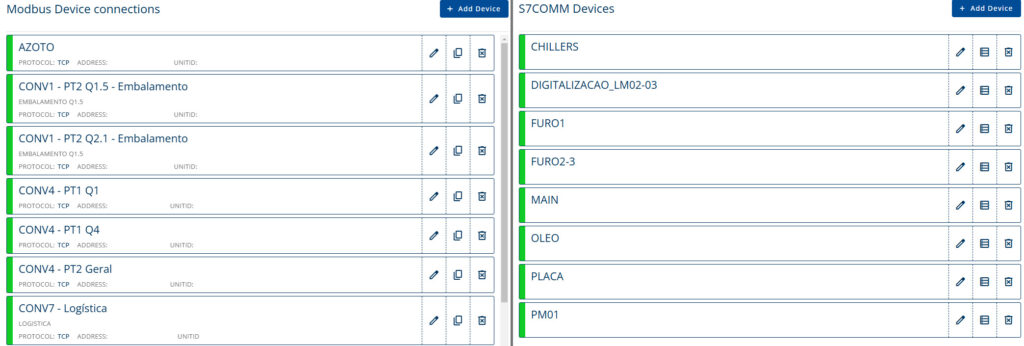
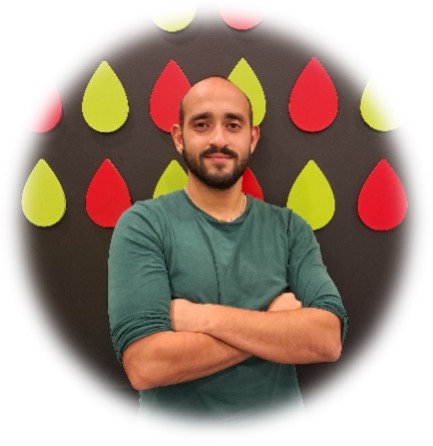
Results and Benefits
By adopting Prosys OPC UA Forge, Casa Mendes Gonçalves achieved several significant results:
- Real-time monitoring of production metrics with Grafana dashboards.
- Reliable integration of diverse machines and systems.
- Improved operational efficiency and scalability.
Reduced downtime and improved decision-making through consistent, accurate data insights.
With real-time data access and better visualization tools, Casa Mendes Gonçalves has already identified multiple opportunities to reduce costs and improve efficiency.
One key benefit has been detecting compressed air leaks in specific zones and machines. By monitoring air consumption during holidays and weekends—when the factory is not operational—the company identified unnecessary air waste and has since been able to locate and repair leaks, reducing unplanned costs.
Similarly, energy consumption tracking has led to operational improvements. With clear insights into electricity usage, employees are becoming more aware of the importance of turning off machines at the end of shifts, helping to reduce unnecessary power consumption.
A third major advantage has been in steam usage optimization. Previously, there was uncertainty about whether an additional steam boiler—costing approximately €110,000—was necessary to support more machines. With precise consumption data now available, Casa Mendes Gonçalves realized that an extra boiler was not needed, preventing a costly and unnecessary investment.
These examples highlight how Prosys OPC UA Forge enables data-driven decision-making, helping the company not only improve efficiency but also avoid unnecessary expenses and optimize resource allocation.
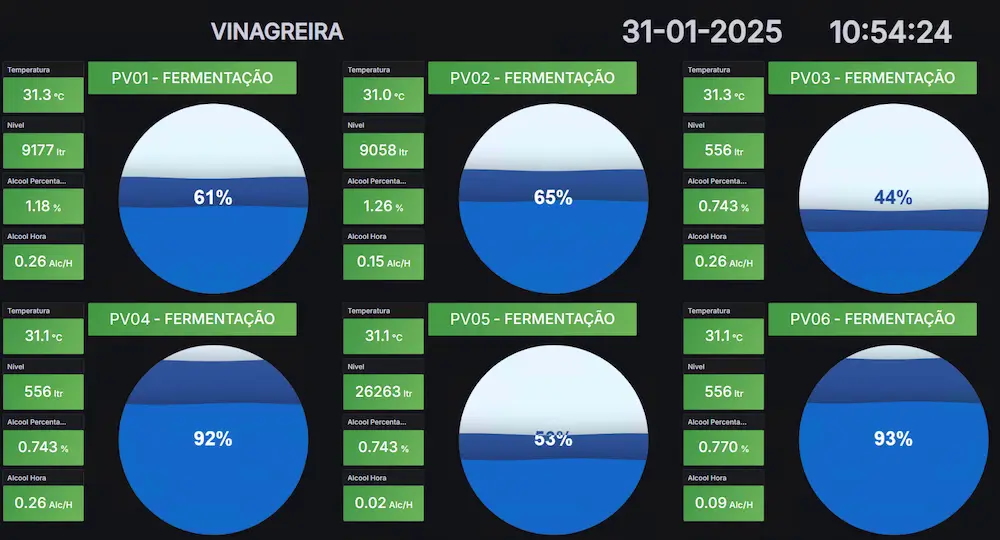
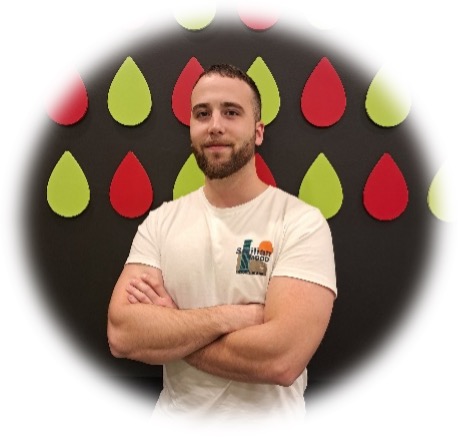
Future Outlook
Casa Mendes Gonçalves plans to expand its solution to additional facilities and is currently evaluating Forge’s capabilities with time-series databases to enhance its system effortlessly. With Prosys OPC UA Forge as the core component of their automation strategy, they are confident in scaling their operations and embracing new technologies.