Harmonizing Technologies: Using UNS and OPC UA Together to Achieve Industry 4.0 Information Design
- 5 min read
Industry 4.0 is all about smart manufacturing: understanding the production process and making it readily available for decision-makers. Unified Namespace (UNS) and OPC Unified Architecture (OPC UA) are key technologies that enable this in practice. This article will explore the capabilities of each and explain how they can be used together to create a complete model of the production process, offering a feasible solution for your industry needs.
UNS
Unified Namespace (UNS) has gotten a lot of attention lately. It represents a conceptual approach to integrating operational technology (OT) and information technology (IT). In UNS, all data sources within a factory are organized on a logical topology. The topology is often similar to ISA-95 topology, which is based on a hierarchy of the enterprise, sites, and areas down to the equipment level. The main idea of UNS is to allow all data within the enterprise to be centrally accessible from a single location for all applications consuming it.
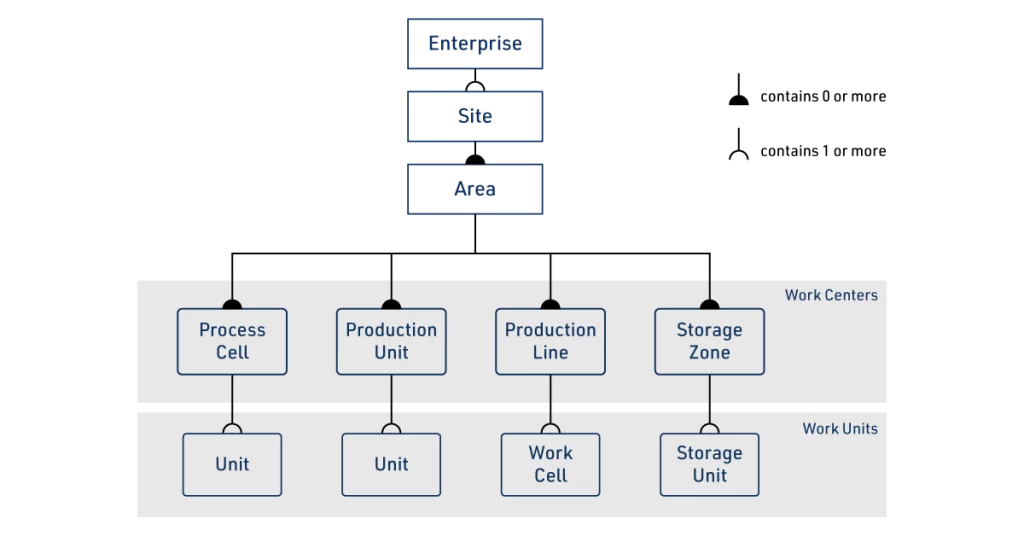
UNS and OPC UA
From a broader perspective, UNS can be viewed as a versatile and vendor-independent concept. It involves a centralized system that provides a standardized interface for data management within a logical hierarchical structure. This adaptability aligns seamlessly with the current state-of-the-art OPC UA client/server setups, where an aggregating OPC UA server, such as our Prosys OPC UA Forge, collects all data from different data sources and represents them in a single information model corresponding to the logical topology. However, organizing all the enterprise’s data under a single OPC UA server is seldom feasible. This is where we will start using UNS.
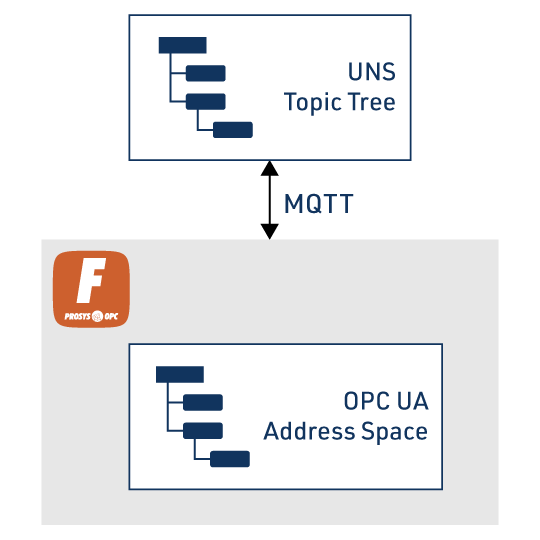
UNS with MQTT
In typical setups, the implementation of UNS uses MQTT. Although MQTT is a client/server protocol, it is referred to more often as a publisher/subscriber model due to the way it is used. MQTT servers (also known as brokers) organize data in a topic hierarchy, and all MQTT clients can publish messages to these topics. At the same time, the clients can subscribe to be notified of new messages. UNS defines how the MQTT topic tree matches the logical structure of the enterprise’s production process. For example, the ISA 95 equipment hierarchy model mentioned above is a common structure for this.
MQTT Challenges
The drawback of plain MQTT is that it does not define the content of the published messages. There are also different topic tree designs being used. Each measurement can be published to its own topic, or topics may be defined per datasets. Those datasets contain all data collected for a piece of complete equipment. The main challenge is that all applications in the MQTT network must somehow understand the topic and message formats used.
OPC UA over MQTT
The traditional OPC UA client/server model successfully makes data available from devices and machines. It can also be extended to larger hierarchies in higher-level gateway applications that aggregate data from several underlying OPC UA servers. The OPC UA Server Address Space is also a hierarchical structure and can contain any model that suits the modeled process. Converting from an OPC UA client/server to a publisher/subscriber communication model will become more feasible at a certain level. Therefore, the OPC Foundation has also defined OPC UA PubSub over MQTT as an alternative that can be used at higher communication levels.
OPC UA PubSub over MQTT uses standardized JSON messages, and the latest version also standardizes parts of the topic tree layout. These make it easy to integrate applications that use OPC UA PubSub over MQTT with each other on different levels of the production hierarchy.
Since most automation systems and industrial equipment are still designed as OPC UA servers, it is straightforward to connect them to a gateway application, such as Prosys OPC UA Forge, and convert the communication to any flavor of MQTT there.
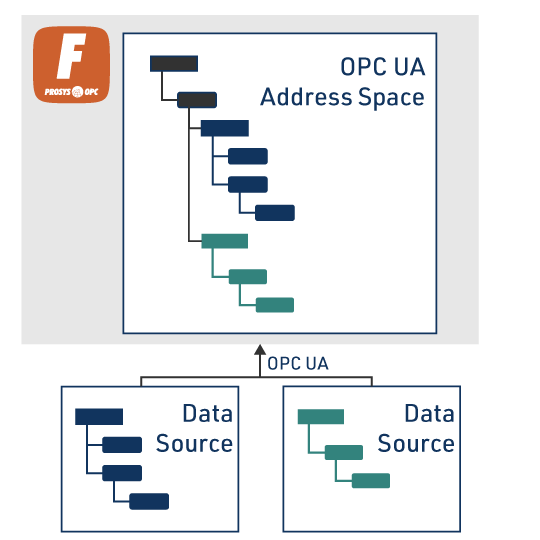
Data Models
Although UNS is all about modeling data within an enterprise, it does not define any models on its own. Also, it is good to understand that different data models are required at various levels of the production process.
OPC UA uses information models to define common equipment and machine data models. This starts from layouts for vendor nameplate information (manufacturer, device model, serial number, etc.) and device health and continues to domain-specific models for machinery, robots, machine tools, etc. By standardizing semantics, OPC UA is way ahead of other industrial technologies. Semantic information is a much more fruitful basis for business analytics than pure data.
Often, data that is readily available from legacy controllers or machines is designed for those specific applications and is not very useful at higher levels of the production process without normalization. Prosys OPC UA Forge can be used to apply OPC UA information models over low-level data and supply additional information to enable the use of the standard models.
Overall, it is entirely feasible to use OPC UA as the base for structuring data to common semantics and UNS to make it available in an enterprise-wide hierarchy from a single source. Of course, different viewpoints are essential to meet the varying needs of various applications.
Conclusion
As we conclude our exploration of Unified Namespace and OPC UA within the context of Industry 4.0, it’s clear that both technologies bring indispensable benefits to the table. While each has its strengths, their integration presents a robust pathway toward genuinely responsive and integrated manufacturing environments. By leveraging the versatility of UNS and the richness of OPC UA information models, industries can achieve higher readiness for advanced business analytics.
The future of industrial automation hinges not on choosing between these different technologies but on understanding how to meld them to suit specific operational needs and challenges effectively. As the landscape of Industry 4.0 continues to evolve, so will the strategies for integrating these pivotal technologies, guiding us toward more adaptive, intelligent, and interconnected industrial systems.
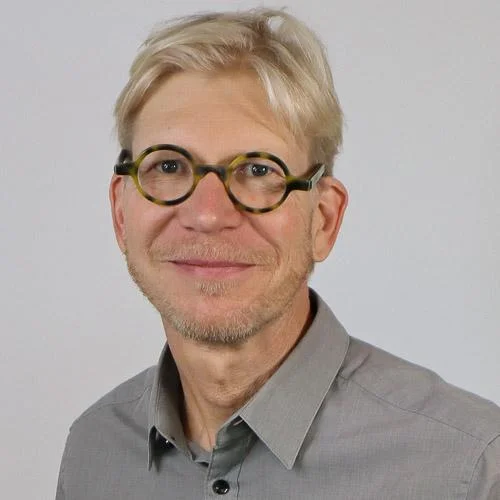
Jouni Aro
Chief Technology Officer
Email: jouni.aro@prosysopc.com