Why Do Standards Matter in Smart Manufacturing?
Introduction
When I envision the future of smart manufacturing, I see auto-configurable systems where devices, machines, and IT systems can be onboarded by simply connecting them to an edge gateway or broker. In this blog post, I will call them EDGE, where all necessary data is available in a standard format.
How could a system automatically configure itself based on the data available in the EDGE?
The answer is standards. Suppose all machines, devices, sensors, and IT systems first identify and publish their data in a standard way. In that case, any connecting system can quickly scan both OT and IT already connected to the EDGE and configure them accordingly. I don’t just mean the OT to IT integration, but also OT to OT and IT to IT integrations. For example, a newly onboarded predictive maintenance system can scan all pumps and valves from the OT network and start monitoring their health. Once it observes a possible break, it creates a service request for the maintenance management system with its standard interface. All this can happen with almost zero integration cost.
Current Situation
Is my vision possible today?
Unfortunately, not on a production scale. This is because too few OT and IT vendors understand the power of standards. On the other hand, the vendors that have recognized the importance of standards have started to push the standards forward and made progress in experiments. The most advanced experiment I’ve seen was the Open Industry 4.0 Alliance’s condition monitoring demonstrator at Hannover Messe 2023, which could detect and display any connected devices using standard communication.
How do I see the situation in five years?
I can confidently say that we will have such systems in production within five years. Not on a vast scale, only with selected early adopter vendors, but yes.
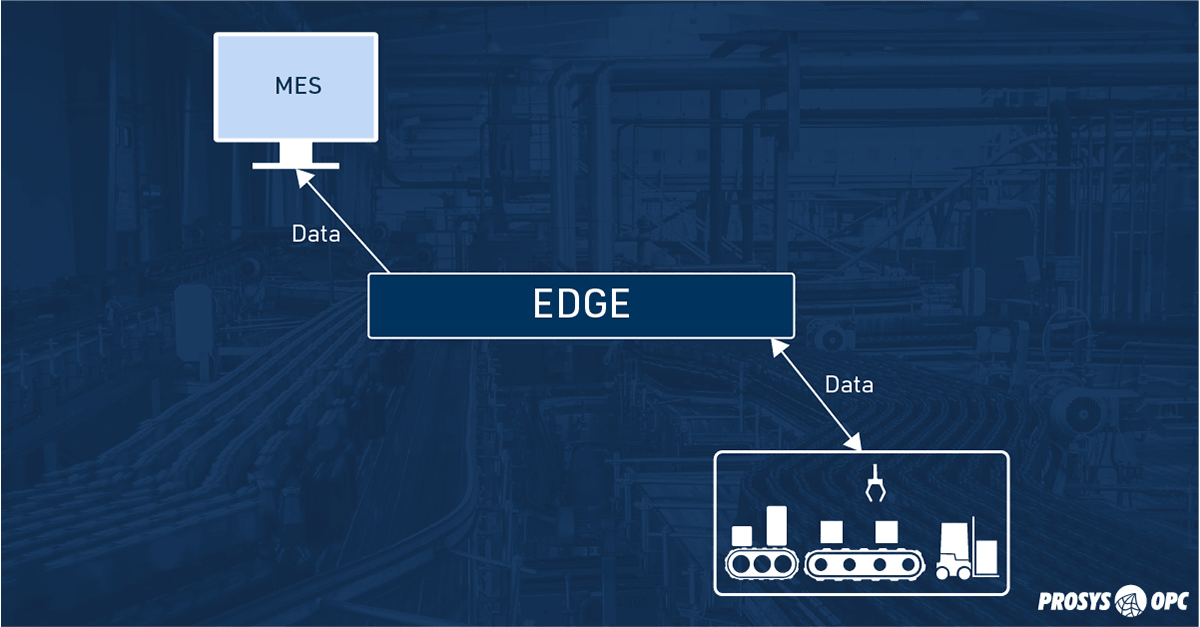
The Future
Five years is a short time, especially in a slow-moving industrial OT and IT world. So, why am I so optimistic?
The most crucial part of the systems, standards, is already on its way. The second most important part is the combination of controllers, IT systems, and EDGE that support the standards. We already have some controllers, such as Siemens S7 and EDGE applications, like our Prosys OPC UA Forge. I have also seen the first IT systems on test benches. Therefore, it is just a matter of time before we see the first success stories, and major vendors will be forced to speed up their development. For manufacturing companies, it will mean some investments to keep up the competitive edge over their rivals, but in the long run, there will be vast savings in integration work.
Conclusion
So, what are the standards I’m talking about?
At Prosys OPC, we are committed to OPC UA in all its flavors. The OPC UA PubSub UDP for Field Exchange, OPC UA Client/Server for reliable and secure OT and OT/IT integrations, and OPC UA PubSub MQTT for scaling OT/IT/Cloud integrations. Given a relatively short time span, I believe the vision above is only achievable with the OPC UA standard family. In conclusion, the standard is here, the controllers are here, the EDGE is here, and IT is enabling auto-configuration while migrating the standards for both communication and the payload.
More Information and Testing
If you have any questions, feel free to directly contact the author, Pyry Grönholm or Prosys OPC Sales using our contact form.
To test Prosys OPC UA Forge, you can request the software download on the product page. For more information about the solution, follow us on social media, which are great options. We’ll be posting tutorials and other interesting details in the coming months.
Author Info

Pyry Grönholm
CEO
Email: pyry.gronholm@prosysopc.com